Application areas:
1, this product is used as VAT dyes, curing dyes and dye color protection agent, ship rust remover and electroplating nickel withdrawal agent, is also dye and vanillin intermediate.
2. Resist S is mainly used as a whitening agent for VAT dye color control printing. Reactive dye printing and pad dyeing color protection agent, can also be used for repairing cloth relief agent reduction dye yarn fabric boiled white protection agent.
3, anti-dyeing salt S is a kind of chemical anti-dyeing agent. VAT dye color anti - dyeing printing, the white cloth first printed anti - white pulp, and then rolled dyed shilin dye. In addition to adding chlorine to the white slurry. Chemical. Zinc (acid anti - dye agent), titanium dioxide. Powder, sometimes also add appropriate amount of anti-dyeing salt S as anti-dyeing auxiliary agent, its principle is to use it has oxidation power, can eliminate shilin dye in the protection /. Risks. / powder reduction force, make the leuco dye body too late fixation on fiber first oxidation for the original dye lake, not with the fiber dyeing effect, namely when the shilin padding liquor cover dyeing cloth on a pattern of the white place, because the white pulp as a resist salt S the existence of oxygen/change/agent, also in the scholastic dyeing liquid/original agent offset, Therefore, it prevents the penetration of shilin dye into cotton fiber, thus enhancing the effect of white pulp prevention.
Resist S features and Functions
ResistS (ResistS) is an auxiliary agent for the direct printing of reactive dyes, and its scientific name is m/NO3.. / /.. Ben /.sulfonate /.acid/sodium, molecular formula is C8H4O5NSNa. The raw materials for preparation are Ben and sulfur. Acid, nitrate, acid, sodium carbonate. Under certain technical conditions, Ben was first used with nitrate. The acid is nitrated to form nitrate. Kiben, followed by sulfur. Acid sulfonation formation between.. Xiao. /. Base... Ben. /. Sulfonated.. Acid, adding sodium carbonate sodium finally, filtering and drying loose powder appearance is yellow, in neutral and alkaline transmitter aerobic/elasticity, used for reactive dye printing paste of organic oxygen / / agent (is a kind of weak oxygen / / agent), its high solubility and dissolution of dye, at the same time of removing acid medium, And the original paste in steam generated by the reducing gas action, prevent reactive dye in printing, steam by printing original paste reducing or reducing gas damage in the steam box, it is the color protection agent in steam, in steam can prevent reducing material damage caused by dye fading or dark. For example, 5-10 g/l Resist S is added to the color paste, which can prevent the fabric fiber from being reductive under high temperature conditions, and prevent the influence of reducing gas in the white pulping on dye color. However, the amount of different reactive dyes is not the same, such as reactive dyes easily affected by reduction, the amount should be increased to 15 grams/l, such as brilliant red K-2G, purple K-3R, and active blue X-Br, D-GR, M-R and other oxidation sensitive reactive dyes with bromoamino as the parent should not be added when used alone, in order to avoid the light fading. In addition, in the printing of corduroy reactive dye, it is required to have a paste with good feel. Generally, sodium alginate pulp is selected, and the thickener FS-86 is used for reactive dye printing, which has the advantages of bright color, permeability, washable, good feel and no gel to black dye. It is used in slurry preparation. The common formula is: to prepare the white paste first, the material is 25 sodium alginate paste 50%, 1%, baking soda 3%, urea 5%, water 37%, stirring and dissolves after adding fS-86 about 4%, stirring and thickening. Then, the appropriate amount of dye and about 20% of the water after fully dissolved, add 80% of the white paste, stir evenly immediately or use. In general, Resist S is still a better oxygen // chemical/agent used in printing pulp. In fabric printing, it is mainly used as anti-dyeing agent, which can prevent dye coloring and form patterns in the process of textile printing and dyeing. In addition, as dye intermediates, other dyes can be synthesized. In fabric printing, the scope of application is mainly as follows.
1. As anti-white additive for VAT dyes
Anti-staining salt S is a chemical anti-staining agent. VAT dye color anti - dyeing printing, the white cloth first printed anti - white pulp, and then rolled dyed shilin dye. In addition to adding chlorine to the white slurry. Chemical. Zinc (acid stain inhibitor), titanium white. Powder, sometimes also join the right amount of reserving salt S as adjuvant of reserving, its principle is to use it with oxygen/force, can eliminate the shilin dyeing insurance powder reduction in force, make the leuco dye body too late on fiber fixation and oxygen/ahead into the original dye lake, not with the fiber dyeing effect, namely when the shilin padding liquor cover dyed in a pattern of the white place in cloth, Due to the anti-white slurry with anti-dye salt S oxygen / / /. The existence of the agent, the reducing agent in the shilin dye offset, so as to prevent the shilin dye soaked into the cotton fiber, thereby improving the effect of white pulp.
2. For copper salt, activity, naftol dyes and other ground color discharge printing color protection agent
Ground color cloth for discharge printing, such as rose, bright red, date red, coffee, autumn green and various fruit colors, before printing, if not through the appropriate amount of oxygen /. Chemical/agent pretreatment and that line printing, often produce relief phenomenon. This phenomenon is caused by the fact that in the process of dyeing, the printing pulp is not completely removed by the scraper, so that there is no pattern on the surface of the ground color cloth, but also can be printed on a little white carving. Powder, resulting in a small amount of white carving. Powder on the ground color of the surface damage and the formation of relief. If there is a drag knife or drag slurry, the relief phenomenon is more serious, which damages the beauty of the fabric surface and forms the appearance defect.
From the chemical analysis, the surface of the ground color is damaged by reducing agent, can be in the ground color on the pre-dip rolled a certain amount of oxygen/chemical./ agent, to resist not scraping white. Powder. But there is a certain amount of oxidant, if it exceeds the capacity of the oxygen/chemical /. Agent, it is superfluous. The powder will break the color of the ground. Therefore, this kind of oxidant only needs to make a certain amount of benefits, but does not need to carve all the white. Powder offset, so that where printing is needed, it can still make the ground color damaged and show the pattern. Anti-stain salt S is this commonly used oxygen/chemical.. Agent. After fabric dyeing drying, dip rolling this 2 ~ 3 g/l solution, generally easy to discharge the color and pattern area of the larger, anti-dyeing salt S dosage can be increased to 5 ~ 6 g/l. Dry and print. After dipping, there is a slight relief or drag knife for printing, so it is white. The powder can be REDOX with the anti-dye salt S without destroying the ground color. But if it exceeds its due capacity, it will still destroy the ground color.
3. Repair fabric relief agent
After cotton printing, if there is dragging knife or embossing phenomenon in many pieces, serious defects will be caused after steam treatment. To overcome this shortcoming, the fabric must be returned to the printing shop for repair immediately before steam treatment. Repair can be based on the degree of relief, the right amount of anti-dyeing salt S(general amount of 0.1 ~ 0.2 g/l) added to the water, with no carving and the surface into fine hemp flower cylinder printing, and then steam treatment, in order to make anti-dyeing salt S and carving white. The effect of powder is improved.
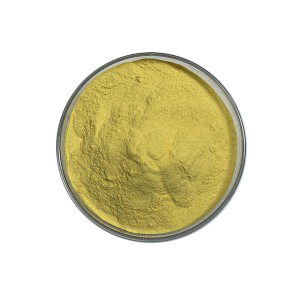
4. For reactive dye printing after steam color protection agent
Reactive dyes are directly printed on cotton cloth after steam, reducing substances or reducing gases in steam machine, and by high temperature steam to promote the hydrolysis of fiber and pulp by reducing, often affect their color light and make it dark. If the printing pulp is added with weak oxygen // chemical // agent anti-dye salt S, when the steam processing after printing, the reducing ability of the steam machine is offset, therefore, the protection of the reactive dye should have a bright color. The amount of the anti-dyeing salt S is generally controlled at about 10 g/l. When the hot setting type and the common type are matched or printed together, the steaming time needs to be longer, which has a greater impact on the color of the common type reactive dye. The amount of anti-dyeing salt S should be increased to 15 g/l. More attention must be paid to the use of a shallow concentration of reactive dye paste on the fabric floor printing, printing pulp must be added to a sufficient amount of anti-dyeing salt S, in order to offset by high temperature steam to promote the fiber and pulp hydrolysis brought by the reductive, to prevent color wilting.
5. As reactive dye pad dyeing - steam method color light protection agent
The presence of reducing gas in the steam chamber will also affect the color of common and thermoset reactive dyes after dyeing by pad dyeing and steam steaming. Dyeing light color is more significant, can be added in the dyeing solution to prevent dyeing salt S about 10 ~ 20 g/l, to prevent color wilting.
6. Used as whiteness protection agent for VAT dyed yarn fabric during scouring
Some VAT dye-colored yarn stripe fabrics such as yarn-dyed striped poplin are often partially peeled and stained with white ground when alkali is boiled. In order to overcome this shortcoming, anti-dyeing salt S can be added to soda scouring solution about 1.5 ~ 3 g/l. Anti-dye salt S is weak oxygen // chemical // agent, can prevent dyes in boiling reduction and infiltration and stain the white ground. This is because the white part of the fabric, due to the protection of salt, will not be affected by the risk of color infiltration and coloring.
Post time: May-23-2022